The 7 Deadly Sinkholes of Continuous Improvement
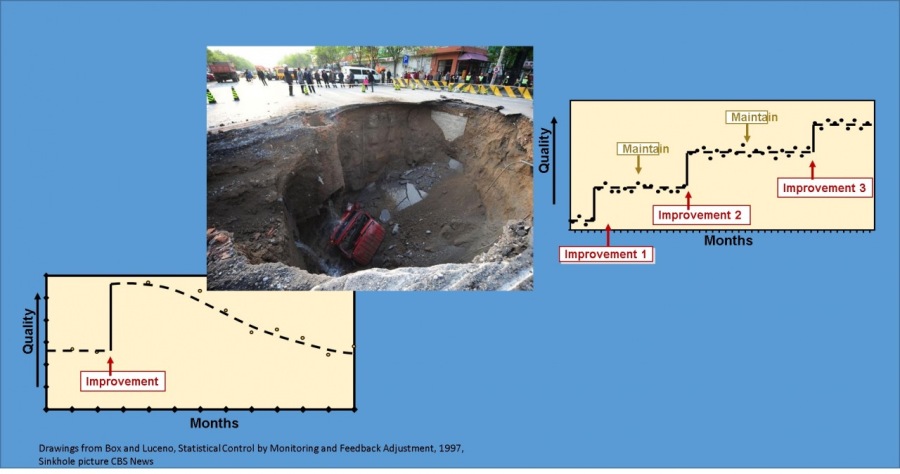
We have now lived through many more iterations of the science of continuous improvement, W. Edwards Demming and Joseph Juran instilling CI in Japanese industry in the 1950s and 60s before returning to reluctant US industry in the 1980s.
CI has been called many labels. In the 1990s Mike Hammer and Jim Champy wrote Reengineering the Corporation based upon working with Ford during the “Quality is Job One” years. Six Sigma grew out of Motorola’s need to keep the Bandit Pager from failing 50% of the time. Lean became popular with the 1990 book The Machine that Changed the World about the Toyota production system.
Virtually every American corporation has at one time or another engaged in a continuous improvement initiative. My Results-Alliance colleague of the last 10 years, Dr. Richard Taylor and I have been involved in many of them.
Unfortunately, lots of CI initiatives fail. After talking with Ric, we’ve come up with some common reasons for those failures. We call them the 7 Deadly Sinkholes of Continuous Improvement:
1. No Improvement mindset. Often people are task focused not process focused; often people think of numbers as a one-time event. This is exacerbated by goal setting systems and to-do lists. But if the improvement mindset doesn’t exist, start by building it.
- Learn to look upstream and downstream of a task for the inputs required and the outputs expected and the effects on other tasks.
- Start to talk about numbers in threes –current performance vs. last year or competition and expected improvement over time
We have now lived through many more iterations of the science of continuous improvement, W. Edwards Demming and Joseph Juran instilling CI in Japanese industry in the 1950s and 60s before returning to reluctant US industry in the 1980s.
CI has been called many labels. In the 1990s Mike Hammer and Jim Champy wrote Reengineering the Corporation based upon working with Ford during the “Quality is Job One” years. Six Sigma grew out of Motorola’s need to keep the Bandit Pager from failing 50% of the time. Lean became popular with the 1990 book The Machine that Changed the World about the Toyota production system.
Virtually every American corporation has at one time or another engaged in a continuous improvement initiative. My Results-Alliance colleague of the last 10 years, Dr. Richard Taylor and I have been involved in many of them.
Unfortunately, lots of CI initiatives fail. After talking with Ric, we’ve come up with some common reasons for those failures. We call them the 7 Deadly Sinkholes of Continuous Improvement:
1. No Improvement mindset. Often people are task focused not process focused; often people think of numbers as a one-time event. This is exacerbated by goal setting systems and to-do lists. But if the improvement mindset doesn’t exist, start by building it.
2. CI is for Them not us. Often leaders “delegate CI.” That never works. Leaders have to start and run projects like everyone else. Running a simple project in a leader’s own area gives them examples to use in talking the talk and shows that they are walking the talk. This will build credibility to direct needed CI work. (See # 3)
3. Working on the wrong stuff. This often starts because leaders delegate CI to the training department: “We first need to build the knowledge and skills of the organization.” People need to bring projects to training and so they do 5S on their computer desktop or a spaghetti diagram of the flow around the water cooler that shows it would be much more efficient by Mary’s desk. Over time people choose projects based upon their personal or departmental interests rather than the priorities of the business. Leaders must say these are our business priorities. These are the processes that support them. This is where we need improvement to meet business goals.
4. CI is for Us not them. CI specialists are a good place to start, but creating a special class of people who do the improvement is death to CI. Six Sigma Black Belts higher level of skill is a good thing, but only with Green Belts and Yellow Belts to help make improvements. Continuous Improvement must ultimately be everyone’s responsibility.
5. It’s all about the certification. I’m all for recognition of skill development, but if this becomes more important than the actual improvement, then the organization is just helping specialists move to their next job.
6. It’s all about BIG projects. In CI training I often say that the real money in CI is in the second and third projects in the same area. Being able to “translate solutions without reinventing the wheel is the biggest gains come from.”
7. We just got tired. Change fatigue is a real thing. Most organizations deal with this by creating new initiatives when the bloom is off the rose of the last initiative. Some say the management theory is “Give them a new ‘bright shiny thing’ and they’ll forget.” In actuality managers get tired too and need to work on something new.
CI isn’t rocket science or brain surgery, but it does take some practice. And as Malcolm Gladwell relayed in Outliers becoming world class takes 10,000 of focused practice, i.e. practice with the sole intent of improvement, in this case improving how you improve.
If an organization sticks with the discipline cost reductions of 30% and similar revenue increases are not uncommon. Getting to that level means avoiding these sinkholesCI isn’t rocket science or brain surgery, but it does take some practice. And as Malcolm Gladwell relayed in Outliers becoming world class takes 10,000 of focused practice, i.e. practice with the sole intent of improvement, in this case improving how you improve.
- Change fatigue presents as arguments about the methodology “What we really need is Lean (or Agile, Work Out, etc.) not Six Sigma.”
- Or change fatigue presents as leaders moving to their next job and the new boss wants to start with a clean slate.
- Or just entropy – the half-life of an initiative gets shorter and shorter and people begin to talk about the “flavor of the month.”
- The answer is in emphasizing results, actual improving bottom-line results that are achieving business objectives. In short integrating CI into the day to day operations of the business.
CI isn’t rocket science or brain surgery, but it does take some practice. And as Malcolm Gladwell relayed in Outliers becoming world class takes 10,000 of focused practice, i.e. practice with the sole intent of improvement, in this case improving how you improve.
If an organization sticks with the discipline cost reductions of 30% and similar revenue increases are not uncommon. Getting to that level means avoiding these sinkholes."
Articles from Alan Culler
View blog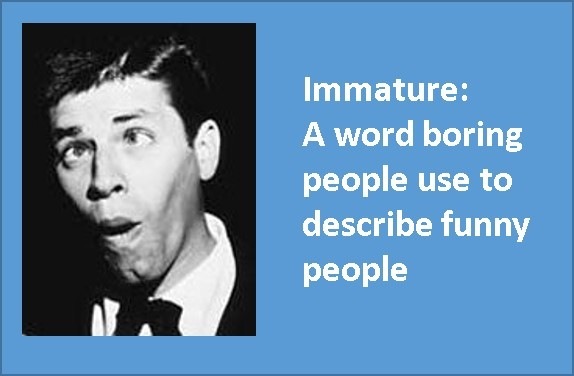
The late, great Jerry Lewis as a young comedian · “You are only young once, Alan, but you can be imm ...
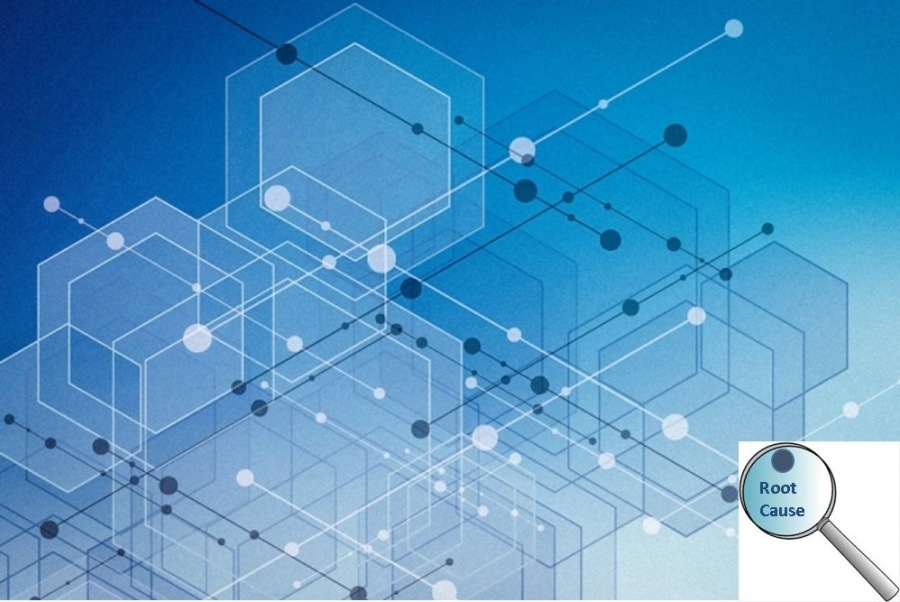
“But we just redid our comp ratios.” · “Look, I don’t care when you did them, I’m telling you your c ...
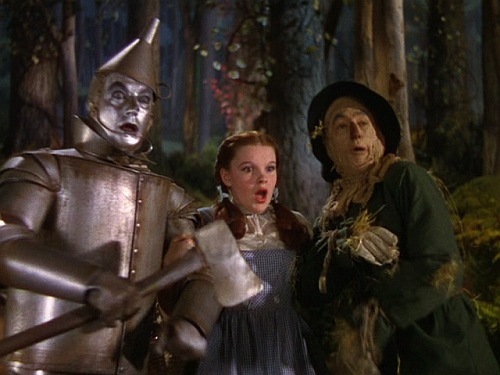
"Lions and Tigers and Bears, oh my!" Jack Haley, Jody Garland, and Ray Bolger in the 1939 MGM film " ...
Related professionals
You may be interested in these jobs
-
Behaviorist
Found in: MyJobHelper US C2 - 14 hours ago
NJ School Jobs Kearny, United StatesKEARNY PUBLIC SCHOOLS · SUPERINTENDENT'S BULLETIN #99 · Behaviorist · Application Deadline: Open until filled · REPORTS TO: · Director of Special Services or designee · DESCRIPTION: · * Must hold a Master's degree in Applied Behavior Analysis, Education, Psychology or related fie ...
-
Automation Controls Engineer
Found in: Appcast US C2 - 5 days ago
Aegis Worldwide Indianapolis, United StatesA family-owned business that designs custom tooling, machinery, and automation systems for some of the world's largest companies, is actively seeking an Automation Controls Engineer who is passionate about the art of crafting top-tier products for a variety of industries (autom ...
-
Travel Cath Lab Tech Contract Gulfport, MS
Found in: Talent US A C2 - 3 days ago
Soliant Gulfport, United StatesMinimum 1+ years Cath Lab experience required. · Exciting Opportunity for Cath Lab Techs in Gulfport, MS · Are you a skilled Cath Lab Tech ready for a fresh and rewarding career opportunity? Your next professional journey is just a heartbeat away · Position: Cath Lab Tech (Contra ...
Comments
Alan Culler
6 years ago #2
I remember liking your comment, Jerry, but I thought I also replied- must not have pressed send - senior moment💀 Thank you for commenting. Glad you liked the title. Improvement is definitely a team task. Apparently CI is harder than it looks - most change is, I guess. Thanks again. Alan
Jerry Fletcher
6 years ago #1